Technologie produkcji narzędzi ściernych Saint-Gobain HPM Polska (część I). Produkcja tarcz do cięcia i szlifowania w kolskim zakładzie Saint-Gobain
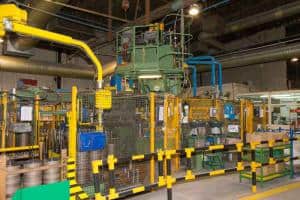
Fabryka Saint-Gobain HPM w Kole należy do największych na świecie producentów żywicznych tarcz do cięcia i szlifowania oraz ściernic ceramicznych. W cyklu kolejnych artykułów, rozpoczynając od produkcji tarcz do cięcia i szlifowania, opowiemy o technologiach stosowanych w tej fabryce.
Saint-Gobain HPM oraz filozofia bezpiecznych narzędzi ściernych
Zanim zajmiemy się technologią produkcji tarcz do cięcia i szlifowania, kilka słów o koncernie Saint-Gobain. Jego początki sięgają drugiej połowy XVIII w. Obecnie jest to jedna z największych międzynarodowych, dynamicznie rozwijających się grup kapitałowych, które działają w sektorze materiałów budowlanych, produkcji opakowań, szkła płaskiego oraz w branży zaawansowanych
Technologia produkcji tarcz do cięcia i szlifowania
Kolski zakład Saint-Gobain HPM przeszedł proces głębokiej reorganizacji i unowocześnienia, dzięki czemu stał się jednym z największych i najnowocześniejszych producentów narzędzi ściernych w Europie. W Kole wytwarzana jest szeroka gama produktów: tarcze tnące i ściernice ceramiczne oraz materiały ścierne nasypowe. Zakład prowadzi też serwis narzędzi diamentowych i maszyn. W naszym cyklu artykułów przyjrzymy się najpierw produkcji tarcz ściernych do cięcia i szlifowania, zwanych niekiedy tarczami żywicznymi (flexami) z powodu głównych składników ich spoiwa, jakimi są właśnie żywice.
Produkcja tarcz rozpoczyna się od przygotowania spoiwa i połączenia go z ziarnem ściernym. Dokładniej mówiąc, najpierw przygotowuje się składniki mieszanki, która w dalszym procesie produkcyjnym zostanie przekształcona w tarczę do cięcia lub szlifowania. Składniki te to sproszkowane żywice, wypełniacze i ziarno ścierne. Jako ziarno w kolskim zakładzie wykorzystywane są elektrokorund, elektrokorund cyrkonowy i ceramiczny. Zanim jednak te składniki trafią na linię produkcyjną, sprawdza się ich jakość w laboratorium zakładowym. Jak wiadomo, jakość wyrobów ściernych zależy nie tylko od prawidłowego przeprowadzenia procesu technologicznego, ale w głównej mierze od jakości ich składników. Jak łatwo zauważyć, jest to zgodne ze zdroworozsądkową zasadą znaną każdej gospodyni domowej, która mówi, że ze złej mąki nie wypiecze się dobrego chleba.
Gdy już mamy odpowiednie ilości wagowe składników ściernicy zgodne ze specyfikacjami technologicznymi, możemy dokładnie je wymieszać. Proces ten przeprowadzany jest na specjalnych automatycznych mieszarkach. Następnie mieszanka trafia do pojemników i zostaje opatrzona odpowiednim opisem zawierającym nazwę narzędzia, które zostanie z niej wytworzone. Jest to konieczne dla prawidłowości kolejnego procesu technologicznego, którym jest prasowanie tarcz.
Proces ten odbywa się na jednym z czterech automatów, na których przez sprasowanie wspomnianej mieszance nadaje jej się formę tarczy ściernej. Każdy automat to w zasadzie rozbudowana, sterowana numerycznie linia produkcyjna agregująca pracę: (1) automatycznych dozowników mieszanek, (2) kilkunastu form kształtowych i odpowiadających im pras wraz z napędami i ich sterowaniem, (3) automatycznych podajników siatek z włókna szklanego i etykiet, (4) automatycznych odbiorników sprasowanych tarcz i (5) manipulatorów służących do umieszczania ich w stojakach z przekładkami wykonanymi ze stalowych dysków. Obsługa czterech automatycznych linii sprowadza się do odpowiednich regulacji dokonywanych na komputerowych panelach sterujących, instalacji i wymiany stalowych form tarcz, dostarczenia surowców: wspomnianej mieszanki spoiwa z ziarnem ściernym, etykiet i siatek z włókna szklanego, które stanowią element wzmacniający każdą tarczę, oraz odbioru sprasowanych tarcz w stojakach z przekładkami. Należy tu wspomnieć, że liczba siatek z włókna szklanego w danym narzędziu i ich wymiary (głównie średnica i grubość) zależą od średnicy i grubości wytwarzanej tarczy.
Sam proces ciśnieniowego formowania tarcz jest automatyczny oraz powtarzalny i przebiega bez udziału człowieka. Ma to bardzo istotne znaczenie dla jego wysokiej jakości, gdyż wyklucza ryzyko popełnienia błędów przez operatorów. Automaty umożliwiają także osiągnięcie bardzo wysokiej wydajności produkcji. W Kole miesięcznie na każdej z czterech automatycznych linii produkuje się ok. 3 mln tarcz.
Sprasowane na automatach i umieszczone w stojakach z przekładkami tarcze transportuje się do specjalnego pomieszczenia, gdzie są suszone. Po wysuszeniu trafiają na paletach do jednego z ośmiu pieców, gdzie są wypalane w temperaturze do 250°C (w zależności od rodzaju tarczy). Na palecie znajduje się do 1000 tarcz (zależnie od grubości i średnicy), zaś pojemność pieców wynosi od 1 do 8 palet. Następnie tarcze są studzone i wyjmowane ze stojaków z przekładkami oraz pakowane i wysyłane do klientów. Każda z partii jest też sprawdzana w laboratorium w celu określenia, czy spełnia założone wymagania jakościowe oraz dotyczące bezpieczeństwa pracy. Testy na rozrywarkach prowadzone są z prędkościami nawet ponad 150 m/s.
Wszystkie produkowane w Kole tarcze do cięcia i/lub szlifowania oznaczone są certyfikatami bezpieczeństwa oSa (Organizacji na Rzecz Bezpieczeństwa Produktów Ściernych) i spełniania europejskiej normy EN 12413-1999. oSa, przyznając swój certyfikat, przeprowadza cyklicznie audyty w kolskim zakładzie produkcyjnym, jak i testy mechaniczne jego produktów końcowych. Natomiast norma EN 12413-1999 definiuje wymagania co do bezpieczeństwa tarcz do cięcia i szlifowania. Na dysku pochodzącym z Koła umieszczane są także inne informacje kluczowe dla bezpieczeństwa pracy narzędziem ściernym. Są to m.in. oznaczenie marki, a także informacje o prędkości obrotowej tarczy, jej kierunku, rozmiarach otworu mocującego oraz terminie przydatności do użycia. Informacja o terminach produkcji oraz przydatności do użycia jest bardzo ważna, ponieważ siła spoiwa tarcz do szlifowania i przecinania ulega zmniejszeniu w miarę upływu czasu. Przestarzały dysk może ulec dezintegracji. Końcowa data „okresu używalności” wyciśnięta jest na centralnym metalowym wieńcu koła. Numer „V” wskazuje kwartał produkcji i tak: V01 – to 1. kwartał, V02 – 2., V03 – 3., a V04 – 4. Np. oznaczenie „V2/2012” umieszczone na wieńcu tarczy oznacza, że dysk nie może być stosowany po końcu drugiego kwartału 2012
Saint-Gobain HPM nie tylko dba o bezpieczeństwo produkowanych narzędzi ściernych, ale także stosuje najwyższe standardy bezpieczeństwa pracy w swoim zakładach, w tym także w kolskim. Np. wszystkie drogi transportowe w nim są oznaczone, zaś pasy poruszania się ludzi rozdzielone od ścieżek przeznaczonych dla wózków widłowych oraz innych pojazdów transportujących surowce oraz gotowe wyroby. Hala produkcyjna jest efektywnie wentylowana, stanowiska pracy odpowiednio zorganizowane, a wszyscy pracownicy mają ochronne ubrania robocze i okresowo odbywają szkolenia na temat zasad oraz praktycznych zagadnień bezpieczeństwa pracy.
Saint-Gobain HPM produkuje w Kole wszystkie rodzaje tarcz do cięcia i szlifowania w średnicach od 100 do 400 mm. W zależności od wykonania przeznaczone są one do obróbki stali konstrukcyjnej, wysoko- i niskostopowej, nierdzewnej (INOX), staliwa, żeliwa, aluminium, tytanu, kamienia, betonu i ceramiki budowlanej (w tym płytek). Ich asortyment podzielony jest na klasy jakościowe:
- standardową (linia Norton STARLINE™),
- profesjonalną (NORLINE™, Norton VULCAN®)
- premium (Blue Fire, QUANTUM).
Podsumowując, Saint-Gobain HPM to nie tylko producent, który stosuje najnowocześniejsze technologie do wytwarzania tarcz do cięcia i szlifowania, aby zapewnić im najwyższą jakość oraz efektywność działania, ale także kompleksowy ich dostawca, który zapewnia zarówno doradztwo techniczne, jak i dotyczące bezpieczeństwa pracy narzędziamiściernymi.