Wiertła udarowe (część II). Konstrukcja wiertła udarowego
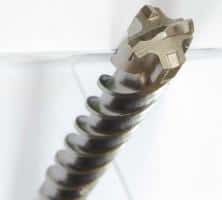
Wiertło udarowe składa się z czterech podstawowych części: główki, zwanej także głowicą (w przypadku większych wierteł), rdzenia, spiralnych rowków i uchwytu.
Jak wspominaliśmy wyżej, główka jest elementem wiertła, który bezpośrednio przekazuje materiałowi obrabianemu energię udaru, czyli wykonuje czynność kruszenia go. Zamocowane są w niej ostrza lub ostrze z węglików spiekanych. Są obecnie dostępne wiertła SDS-plus, które mają główki całkowicie wykonane w węglików spiekanych, których liczba ostrzy dochodzi do pięciu. Ostrza węglikowe przeważnie lutuje się do głowicy wiertła. I od stosowanej technologii lutowania zależy w dużym stopniu trwałość tego narzędzia. Rozróżnia się: (1) lutowanie i
hartowanie w piecu przelotowym (najtańsza technologia, co oznacza też niską jakość wiertła), (2) lutowanie indukcyjne (daje nieco lepszą jakość), (3) lutowanie próżniowe (metoda stosowana w produkcji wierteł o dużych średnicach) i hartowanie, (4) lutowanie AWB i hartowanie (technologia zoptymalizowana pod względem średnicy narzędzia, dająca mu dużą wytrzymałość i obniżająca drgania podczas wiercenia). Głowice całkowicie wykonane z węglików spiekanych mocuje się do korpusu wiertła za pomocą technologii łączenia dyfuzyjnego. Technologia ta zapewnia bardzo mocne połączenie wiertła i głowicy, dzięki czemu można nim wiercić w żelbetonie. Bardzo ważnym czynnikiem wpływającym na trwałość wiertła jest rodzaj węglików spiekanych użytych na ostrza. Są one mieszaniną węglika wolframu, kobaltu i tzw. naturalnych domieszek. Im więcej w tej mieszance jest węglika wolframu, tym mniejsza wielkość ziaren i wyższa odporność oraz dłuższa żywotność ostrza.
Należy tu zauważyć, że średnica główki jest nieco większa niż średnica spirali rowkowej, czyli tzw. korpusu wiertła. Przyczyną tego jest konieczność zmniejszenia jego tarcia o obrabiany materiał, aby móc jak najefektywniej wykorzystać energię udaru generowaną przez napędzające elektronarzędzie i umożliwić najefektywniejsze odprowadzanie urobku.
Zadaniem rdzenia jest zapewnienie wiertłu osiowej pracy i efektywna transmisja energii udaru od uchwytu do głowicy. Spiralne rowki, zaczynające się w głowicy, oplatające rdzeń i kończące się w uchwycie, przeznaczone są, jak już wspominaliśmy, do usuwania urobku z wykonywanego otworu. Spirala, oczywiście, bierze też udział w przekazywaniu energii udarowej, a więc pełni dwie wspomniane role. Mamy różne wykonania spirali: standardowa 2-zwojna L (stosowana w standardowych wiertłach SDS-plus), 2-zwojna U (dobre odprowadzanie urobku podczas wiercenia w materiałach abrazyjnych), 2-zwojna optymalizowana (przyspiesza wiercenie i zmniejsza tarcie), 2+2-zwojna (zoptymalizowana pod względem drgań, dająca lepsze przenoszenie energii udarowej na głowicę, stabilizuje wiercenie i umożliwia szybsze odprowadzanie większych wiórów metalowych podczas obróbki żelbetonu), 4-zwojna standardowa (daje dużą wytrzymałość wiertłu i stabilizuje proces wiercenia), 4-zwojna optymalizowana (daje szybsze odprowadzanie urobku i zwiększa trwałość narzędzia). Rdzeń ze spiralnymi rowkami, czyli korpus narzędzia, wytwarzany jest ze stali chromowo-niklowo-molibdenowej. Jest ona na tyle twarda i sprężysta, iż umożliwia efektywne przenoszenie energii udaru oraz momentu obrotowego wrzeciona elektronarzędzia.
Główną funkcją uchwytu wierteł udarowych jest ich pewne zamocowanie w maszynie, zaś jego zadaniem – transmisja do narzędzia energii udaru oraz obrotów (momentu obrotowego) wytworzonych przez elektronarzędzie. Obecnie wiertła udarowe wykonuje się z różnymi uchwytami, przy czym narzędzia przeznaczone do wiertarek udarowych mają jedynie uchwyt w formie wydłużonego walca, tzw. walcowy, lub tzw. CYL (patent Boscha), czyli uchwyt cylindryczny z wypustem uniemożliwiającym obracanie się narzędzia w uchwycie wiertarskim. Zaś wiertła udarowe do młotków elektropneumatycznych posiadają specjalnie profilowane uchwyty: SDS-plus, SDS-max, sześciokąt 13 mm (SW 13) lub 19 mm (SW 19) oraz wieloklin.
Ta duża liczba rodzajów uchwytów wierteł udarowych stosowanych w młotkach elektropneumatycznych wynika z faktu, że muszą one swoją wielkością odpowiadać pewnemu zakresowi średnic tych narzędzi i być dostosowane do transmisji energii udarowej o różnej wartości, jak również z różnych standardów mocowań wykorzystywanych dotychczas przez producentów elektronarzędzi.
Niewątpliwie najbardziej popularnym obecnie standardem jest system SDS, umożliwiający szybkie mocowanie narzędzi. W
Wiertła systemu SDS-plus o średnicy uchwytu 10 mm mają cztery wpusty. Dwa z nich w kształcie przypominającym fasolki służą do pewnego mocowania wiertła, jednocześnie zapewniając pewien poosiowy luz umożliwiający mu wykonywanie pracy udarowej, czyli ruchów wzdłuż jego osi. Następne dwa podłużne wpusty przeznaczone są do nadawania wiertłu obrotów. Uchwyt SDS-max jest większy niż SDS-plus, ma średnicę 18 mm i służy do wiercenia otworów o średnicach od 12 do 155 mm. Posiada nie cztery, a pięć wpustów, dwa z nich o kształcie fasolek przeznaczone są do mocowania narzędzia, a trzy podłużne do przekazywania mu obrotów silnika elektrycznego młotka. W systemie SDS oddzielono funkcje blokady wiertła i przenoszenia momentu obrotowego. Dzięki temu uzyskano pewniejsze osadzenie wiertła i dużą powierzchnię stykową z mocowaniem w młotku. Efektem tego jest znaczne zmniejszenie zużycia uchwytu wiertła. Warto także zwrócić uwagę, że praca przy użyciu młotków elektropneumatycznych z systemem SDS odbywa się mniejszym nakładem siłoperatora.