Prawidłowe ustawienie noży w nożycach do blachy
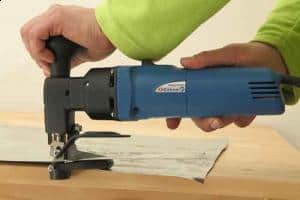
Niezmiernie istotne dla prawidłowej i efektywnej pracy nożycami nożowymi jest odpowiednie ustawienie noży tnących. Niniejszy artykuł podaje podstawowe zasady regulacji ich rozstawienia.
Nożyce nożowe to elektronarzędzia wymagające dokonania odpowiedniej regulacji rozstawu noży zarówno w płaszczyźnie poziomej (horyzontalnej), jak i pionowej (wertykalnej) w celu dostosowania ich do obrabianej grubości. Dlatego za każdym razem, gdy tniemy blachę o innej grubości, należy dokonać regulacji rozstawienia noży. W tym celu trzeba posłużyć się szczelinomierzem. Wielkość rozstawu horyzontalnego ma wpływ na skuteczność cięcia nożycami. Jeśli odległość pomiędzy nożami w płaszczyźnie poziomej za
Aby prawidłowo ustawić rozstaw noży, należy poluzować nóż nieruchomy. Następnie między noże włożyć szczelinomierz (fot. 1.), w naszym wypadku jest to pasek o grubości 0,05 mm, gdyż blacha, którą chcemy przeciąć, ma grubość 0,5 mm. Po ustaleniu prawidłowej odległości, montujemy nóż (fot. 2.) i blokujemy jego pozycję (fot. 3.), a na końcu spomiędzy ostrzy wyjmujemy szczelinomierz. Teraz możemy przejść do ustawienia noży w pozycji pionowej.
Przypomnijmy, rozstaw w płaszczyźnie pionowej (czyli wertykalny) to maksymalna odległość między nożami (tj. mierzona w punkcie najwyższego położenia noża ruchomego). Dlatego potocznie nazywa się go wysokością cięcia. Determinuje on wydajność pracy. Największa wysokość cięcia z możliwych to taka, przy której blacha nie ślizga się pomiędzy dwoma ostrzami w ich pozycji maksymalnego rozstawienia. Zatem prawidłowa wysokość jest nieznacznie mniejsza od grubości obrabianej blachy. Kiedy zaś jest większa lub równa grubości blachy, czyli za duża, dochodzi do wpychania się ciętego arkusza między noże. W takim przypadku użytkownicy często tną tylnym odcinkiem ostrzy noża ruchomego, jeśli wywierają zbyt duży posuw nożycami. To zaś powoduje za duże obciążenie tylnych krawędzi tnących i często doprowadza do złamania noża ruchomego albo do zbyt dużej deformacji blachy w miejscu cięcia. Jeżeli wysokość cięcia jest zbyt mała, następuje zmniejszenie długości cięcia na jednym suwie noża, a w konsekwencji do spadku szybkości cięcia, czyli de facto mniejszej wydajności.
Po tym wstępie teoretycznym przystąpmy do regulacji wysokości rozstawu noży. Mając prawidłowy rozstaw noży, możemy więc je ustawić w pozycji pionowej. W tym celu ustawiamy nóż ruchomy w punkcie najwyższego jego położenia (w tym celu czasami konieczne jest parokrotne włączenie i następnie wyłączenie nożyc, aby ostrza ustawiły się w tej pozycji) i luzujemy go. Potem ustawiamy prawidłową wysokość noża zgodnie z rys. 1. za pomocą górnej śruby blokującej (fot. 4.) i montujemy nóż kluczem imbusowym (fot. 5.), dokręcając śrubę mocującą. Gdy mamy prawidłowo ustawione noże (fot. 6.), możemy przystąpić do cięcia (fot. 7.).