Na jakości nigdy się nie traci
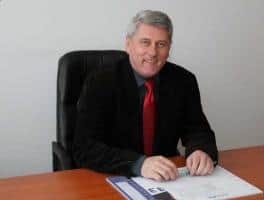
O specyfice wytwarzania artykułów ściernych oraz jakości i powtarzalności w procesie produkcji rozmawiamy z Wojciechem Sitkowskim – dyrektorem naczelnym Techniflex Sp. z o.o. w Mszanie Dolnej.
Zakład Produkcji Artykułów Ściernych w Mszanie Dolnej to przedsiębiorstwo z tradycjami i wieloletnią historią. – Firma powstała w 1955 r. jako zakład zajmujący się produkcją galanterii drewnianej. Przez kilka lat wytwarzano tu głównie dębowe beczki – wspomina Wojciech Sitkowski, dyrektor naczelny Techniflex Sp. z o.o. – Od 1967 r. rozpoczęto wyrób tarcz zdzierakowych i przeznaczonych do szlifowania oraz cięcia. Ta część działalności szybko zdominowała
inne i wkrótce stała się jedyną specjalnością fabryki, zaś jej wyrobyzdobyły uznanie na rynku polskim, a także na rynkach zagranicznych.Zakład dysponuje nowoczesnym parkiem maszynowym. – Pracujemy na maszynach marki Maternini – informuje Wojciech Sitkowski – Ta włoska firma specjalizuje się w produkcji urządzeń i oprzyrządowania do wytwarzania tarcz ściernych. Mamy również jeden z najlepiej wyposażonych działów eksploatacyjnych w Polsce, oprzyrządowany w najnowocześniejsze automaty do kontroli wytrzymałości dynamicznej i wydajnościowej tarcz, a także w maszyny do niezależnego sprawdzania skrawalności i eksploatacji ściernicy. W oparciu o to laboratorium i, oczywiście, świetnych fachowców jesteśmy w stanie codziennie sprawdzać jakość wytwarzanych przez nas tarcz i w razie potrzeby optymalizować proces ich produkcji. Kładziemy bardzo duży nacisk na bezpieczeństwo wyrobów, które trafiają
do użytkowników. Ściernice, które wychodzą od nas z zakładu, rozrywają się dopiero przy dwa razy większych obrotach niż te, przy których pracują w rzeczywistości.Wszystkie etapy produkcji i testów tarcz są rejestrowane w systemie informatycznym stworzonym specjalnie na potrzeby zakładu. – Jesteśmy jedynym zakładem w Europie, a może i na świecie, w którym każda ściernica ma tak dokładny numer identyfikacyjny – podkreśla Wojciech Sitkowski. – Oznaczenie to informuje, kiedy ściernica została wyprodukowana, na której zmianie, na której maszynie, z jakiego surowca, jaką miała wytrzymałość dynamiczną i jak przeszła testy eksploatacyjne. Numer powiązany jest ze specyfikacją, która przechowywana jest w zakładzie w formie elektronicznej i papierowej przez 10 lat. Dlatego każda tarcza przyniesiona do nas z rynku może być dokładnie sprawdzona. Firma posiada certyfikaty jakościowe: ISO 9001 i ISO 14001, jest zakładem bardzo bezpiecznym dla środowiska. – W tej chwili jesteśmy w trakcie wdrażania znaku oSa (Organizacji Bezpieczeństwa Narzędzi Ściernych) – jest to niemiecki znak bezpieczeństwa, który otwiera drzwi do wszystkich rynków na świecie.
Jak podkreśla Wojciech Sitkowski, oferta Technifleksu jest kompleksowa: – Naszą marką wiodącą jest IncoFlex. Jesteśmy jednym z dwóch czy trzech zakładów w Polsce, który produkuje, oprócz standardowych tarcz do cięcia i szlifowania (od ø 100 do ø 230 mm) oraz do cięcia na przecinarkach stacjonarnych (od ø 300 do ø 500 mm), także ściernice zdzierakowe na spoiwie żywicznym, używane do obróbki zgrubnej, głównie w odlewnictwie. Wszystkie ściernice zdzierakowe produkujemy na indywidualne zamówienia, w różnych wielkościach (od 6 cm do 120 cm) i kształtach. To jest asortyment, który mocno się rozwija. Regularnie wprowadzamy w nim nowe rozwiązania i wyroby. Produkujemy też ściernice listkowe oraz lamelkowe o różnych granulacjach.
Klienci firmy mogą liczyć na wsparcie techniczne (doradcze), a także marketingowe. – Dobór ściernic nie jest rzeczą prostą, dlatego bardzo mocno koncentrujemy się na wsparciu technicznym wszystkich naszych klientów – zapewnia Wojciech Sitkowski. – Mamy świetnie wyposażony serwis mobilny, który cały czas doposażamy. Dzięki temu możemy właściwie w każdym miejscu zademonstrować możliwości naszych produktów, porównać je z wyrobami konkurencyjnymi. Regularnie przeprowadzamy także szkolenia dla przedstawicieli naszych klientów. Takie spotkanie kursowe trwa zazwyczaj od 5 do 7 godz., w jego trakcie prezentujemy proces produkcyjny, znakowanie tarcz, kontrolę jakości i testy eksploatacyjne. Po takim szkoleniu nasi partnerzy nabierają pewności co do jakości i bezpieczeństwa sprzedawanych wyrobów. Bardzo często uczestniczymy również w dniach otwartych u naszych partnerów, regularnie bierzemy udział w targach branżowych w Polsce, a co dwa lata prezentujemy się na wystawie w Kolonii.
Można powiedzieć, że w 2011 r. Zakład Produkcji Materiałów Ściernych w Mszanie Dolnej narodził się na nowo. Nie zapominając o szacunku dla tradycji, wprowadzono nowe zasady i procedury, zrestrukturyzowano proces produkcji. Wyznaczono też nowe cele do osiągnięcia. – Utrzymanie stabilnej pozycji w kraju i zdobywanie nowych rynków eksportowych to nasze podstawowe zadania na najbliższe lata. Myślę, że jesteśmy je w stanie z powodzeniem zrealizować. Nie zapominamy również o opracowywaniu i wprowadzaniu do naszej oferty nowych produktów, a także o ciągłym doskonaleniu procesu produkcyjnego. Wysoka jakość naszych produktów jest naszą przyszłością – konkluduje Wojciech Sitkowski
*Na zdjęciu głównym nasz rozmówca: Wojciech Sitkowski – dyrektor naczelny Techniflex Sp. z o. o. w MszanieDolnej