Czy wiercenie w stali musi być uciążliwe?
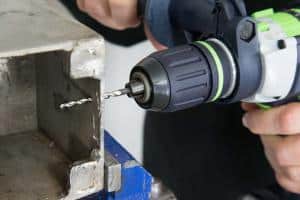
Wiercenie w stali wykonywane za pomocą wiertarek ręcznych może się stać czynnością bardzo uciążliwą, jeśli użyjemy do tego wierteł o nieodpowiedniej geometrii. Zastanówmy się więc, jakie wiertła najlepiej zastosować do tego typu operacji.
Oczywiste jest, że do wiercenia w stali używa się wierteł krętych specjalnie przeznaczonych do tego typu obróbki. Jednakże wiele osób, które muszą wykonywać otwory w stali, narzeka, że chociaż używa do tego prawidłowych narzędzi, jest to operacja długotrwała i wymagająca użycia dużej siły nacisku na wiertarkę, a więc męcząca. Można więc zapytać, skąd wynika konieczność stosowania tak dużej siły? Najprościej można
odpowiedzieć, że – z geometrii wierteł. Wiertła standardowe mają bowiem najprostszą z możliwych geometrię krawędzi skrawających, czyli skręcone krawędzie stożkowate, połączone krawędzią poprzeczną zwaną ścinem. Znajduje się on na samym wierzchołku osi wiertła. Konsekwencją tego usytuowania jest bliska zeru prędkość obwodowa ścina. Jego krawędź tnąca jest do tego tępa i dlatego bierze niewielki udział w procesie wiercenia. W zasadzie szlifuje tylko powierzchnię obrabianego metalu. Ponieważ ścin nie jest ostry, nie centruje wiertła, pozwalając zbaczać mu z wyznaczonego punktu wiercenia w pierwszej fazie wykonywania otworu (tylko podczas wiercenia ręcznego). Na skutek tego dochodzi często do zarysowania powierzchni elementu, w którym wiercimy.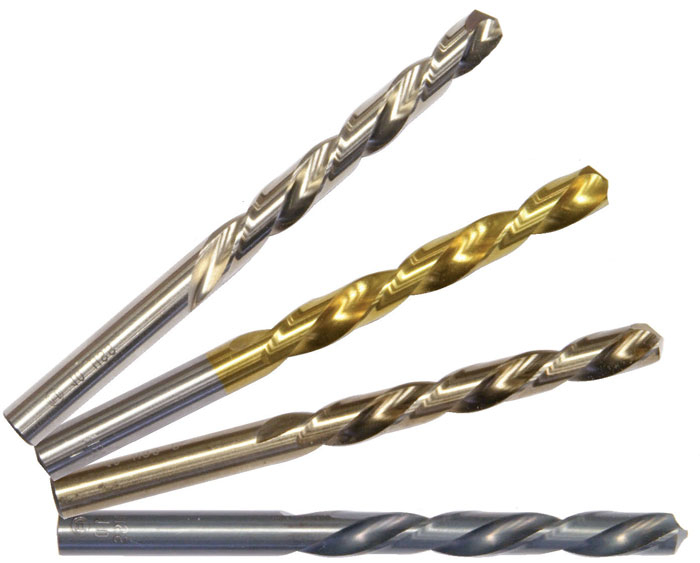
Aby do tego nie dopuścić, musimy wywierać mocny docisk na narzędzie. Badania wykazały, że do 60% siły nacisku zużywane jest na pokonanie oporu, który metal stawia ścinowi. Duża siła nacisku i tarcie w strefie skrawania są przyczynami powstawania w niej wysokiej temperatury. Aby temu zapobiec, musimy stosować chłodzenie. Stąd, jak widać, krawędź ścina jest przyczyną wielu kłopotów z wierceniem w metalach, szczególnie w twardej stali. Jedną z metod radzenia sobie z nimi jest stosowanie wierteł o zoptymalizowanej geometrii, która eliminuje konieczność stosowania dużej siły, jednocześnie zwiększając szybkość wiercenia w metalach.
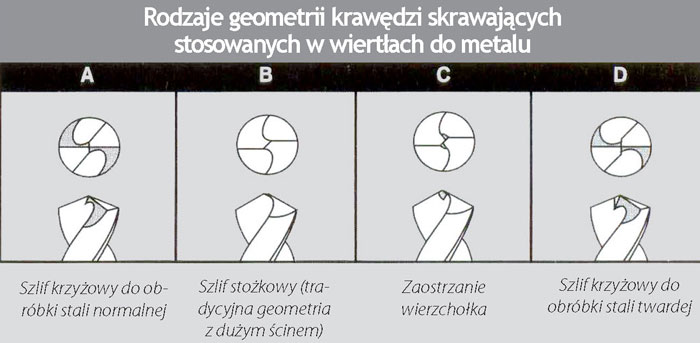
Aby sprawdzić, jak skuteczne jest wiercenie wiertłami o zmodyfikowanej geometrii krawędzi skrawających ostrzy, wykorzystaliśmy do tego wiertła: HSS (o zmodyfikowanej geometrii typu A (zob. rysunek zamieszczony w artykule), HSS TiN (wiertła HSS pokryte azotkiem tytanu o zmodyfikowanej geometrii typu A) i kobaltowe HSS-Co (o zmodyfikowanej geometrii typu D) i porównaliśmy otrzymane wyniki z wynikami użycia popularnego wiertła HSS o tradycyjnej geometrii typu B, czyli z dużym ścinem. Wszystkie użyte przez nas narzędzia miały średnicę 10 mm. Wykonywaliśmy nimi otwory o głębokości 10 mm w stali konstrukcyjnej przy użyciu wiertarki 1000-watowej. Stosowaliśmy nacisk wiertłem na obrabiany element stalowy przez obciążenie dźwigni stojaka wiertarskiego sztabą stalową o wadze 10 kg. Wiercenie było więc wykonywane bez udziału operatora, przez co zostały wyeliminowane czynniki przypadkowe towarzyszące ręcznemu wykonywaniu tej operacji. Rola operatora sprowadzała się tylko do włączenia i wyłączenia wiertarki oraz do podawania emulsji chłodząco-smarującej do strefy wiercenia.
Wiertłem HSS o zmodyfikowanej geometrii A uzyskaliśmy następujące czasy: 18 s (10 kg) i 16,25 s (10 kg); zaś HSS TiN o geometrii A – 9 s (10 kg) i 9 s (10 kg); HSS-Co o geometrii D – 21 s (10 kg) i 14 s (10 kg). Otwory porównawcze wykonane wiertłem HSS o tradycyjnej geometrii typu B zostały wywiercone w następujących czasach: 1 m 07 s (10 kg) i 54 s (10 kg).
Otrzymane wyniki pokazują, że wiertłami o zmodyfikowanej geometrii możemy wiercić nawet do ponad 6 razy szybciej niż wiertłami o tradycyjnej geometrii, a także, że w przypadku wykonywania otworów w stali konstrukcyjnej najbardziej wydajne są wiertła HSS TiN z geometrią typu A. W tego typu obróbce są one ponad 50% wydajniejsze niż wiertła kobaltowe, które odznaczają się bardzo wysoką trwałością, co wynika z właściwości użytego na nie materiału. Powodem szybszej pracy wierteł HSS TiN jest zmniejszenie tarcia w strefie skrawania
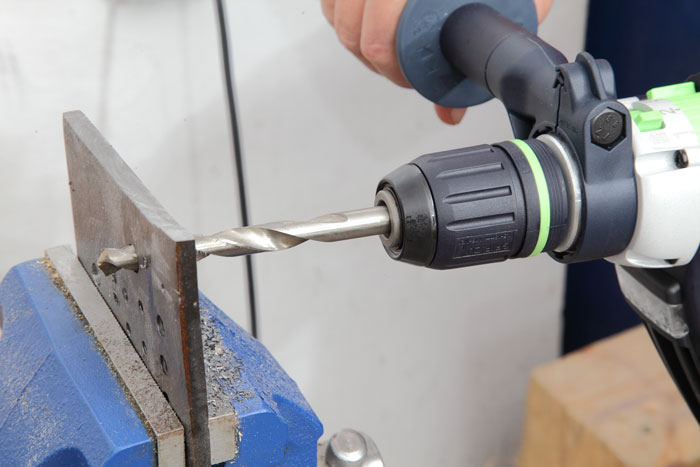
Reasumując, można powiedzieć, że gdy musimy wiercić w stali z ręki, najlepiej jest używać wierteł o zmodyfikowanej geometrii, gdyż wtedy znacznie skrócimy proces wykonywania otworu, a tym samym nie będzie on dla nas bardzo uciążliwy. Wniosek ten szczególnie dotyczy osób, które do tego używają wiertarko-wkrętarek niemających rękojeści dodatkowych. Muszą one wywierać dość duży nacisk maszyną, co jest niewygodne i doprowadza do odchylania wiertła od wyznaczonej osi wiercenia. W efekcie uzyskany otwór jest małej jakości, a w czasie wiercenia wielokrotnie dochodzi do zakleszczenia się wiertła w obrabianym materiale, co jest przyczyną przeciążenia elektronarzędzia i ma negatywny wpływ na jegotrwałość.