AKADEMIA ŚLUSARSTWA (CZĘŚĆ VII). PROSTE WARSZTATOWE PRZYRZĄDY I NARZĘDZIA POMIAROWE
Niezależnie od wielkości produkcji niezbędnym składnikiem procesu technologicznego jest kontrola jakości wykonywanych elementów i części maszyn. Podstawowym celem pomiarów warsztatowych jest sprawdzenie zgodności wymiarów i kształtu obrabianego przedmiotu z rysunkiem technicznym.
Pomiar polega na praktycznym wyznaczeniu danej wielkości (z określoną dokładnością) badanego elementu i porównanie tej mierzonej wielkości z wartością przyjmowaną jako jednostka miary. Na przykład mierzoną długość porównujemy do 1 mm lub 1 m, a zważoną masę ciała do 1 g lub 1 kg. Sprawdzenie kształtu przedmiotu polega m.in. na pomiarze długości krawędzi lub wielkości kątów pomiędzy powierzchniami. Należy pamiętać, że otrzymane wyniki pomiarów obarczone są pewnym błędem, czyli różnicą
między wartością zmierzoną a wartością rzeczywistą określonej wielkości. Przyczynami błędów mogą być m.in. nieodpowiednie metody pomiaru, niedokładności przyrządów pomiarowych, niedoskonałości narządu wzroku człowieka czy warunki otoczenia (temperatura, drgania) w którym odbywa się pomiar. Na ogół zaleca się aby pomiary były wykonywane w temperaturze około 20°C.Narzędzia pomiarowe podzielone są na dwie grupy: wzorce miar i przyrządy pomiarowe. Do wzorców miar zaliczamy te narzędzia pomiarowe, które odtwarzają znaną wartość danej wielkości, np. przymiar kreskowy pokazuje bezpośrednio wynik pomiaru w milimetrach, a odważnik na szalce wagi informuje bezpośrednio o masie ważonego ciała. Do grupy wzorców zaliczamy też płytki wzorcowe, szczelinomierze, promieniomierze, kątowniki, wałeczki pomiarowe. Z kolei przyrządy pomiarowe mają przetworniki, które przetwarzają jedną wielkość w inną (np. w tradycyjnym termometrze wzrost objętości rtęci informuje o temperaturze w stopniach Celsjusza) lub powiększają dokładność odczytywania wyniku pomiaru, np. za pomocą noniusza suwmiarki.
Do pomiarów mniej dokładnych często używa się prostego wzorca długości, jakim jest przymiar kreskowy z podziałką milimetrową (rys. 1). Przymiar kreskowy ma postać listwy lub taśmy stalowej o długości od 150 do 1000 mm. Niektóre przymiary na drugiej krawędzi mają podziałkę zaznaczoną co pół milimetra. Przymiar kreskowy jest także narzędziem często stosowanym podczas trasowania na płaszczyźnie.
Do sprawdzania płaskości niewielkich powierzchni stosuje się liniały krawędziowe (rys. 2). W zależności od wielkości sprawdzanej powierzchni stosuje się liniał o określonej długości (w kompletach znajduje się kilka liniałów o różnej długości). Jedna powierzchnia czołowa liniału jest ścięta pod kątem 90°, a druga pod kątem 45°, aby umożliwić sprawdzenie płaskości powierzchni zespolonych pod kątem ostrym. Krawędź robocza liniału jest minimalnie zaokrąglona (0,1–0,2 mm) i po przyłożeniu do sprawdzanej powierzchni umożliwia obserwację szerokości świetlnej szczeliny. Aby za pomocą szczelinomierza określić płaskość powierzchni, należy liniał przykładać do sprawdzanej powierzchni w różnych kierunkach i miejscach i obserwować czy występuje szczelina świetlna między krawędzią liniału a sprawdzaną powierzchnią. Lekkie pochylenie liniału ułatwia obserwację szczeliny świetlnej.

Rys.1. Przymiar kreskowy (źródło: www.elektro-met.pl/pl/p/Przymiar-kreskowy)

Rys.2. Liniał krawędziowy (źródło: https://pl.wikipedia.org/wiki/)
Bardzo często wzornikami stosowanymi w warsztatach produkcyjnych i laboratoriach są kątowniki służące do sprawdzania kąta prostego (rys. 3). Najczęściej spotyka się kątowniki płaskie z grubym jednym ramieniem, ze stopą lub krawędziowe, rzadziej natomiast kątowniki walcowe. Podczas sprawdzania kąta prostego zewnętrznego należy przyłożyć kątownik wewnętrznymi bokami ramion do obrobionych powierzchni przedmiotu i obserwować wielkość szczeliny świetlnej. Odwrotnie, w celu sprawdzenia kąta wewnętrznego kątownik przykłada się bokami zewnętrznymi.
Szczelinomierz składa się zestawu cienkich płytek i służy do określania wymiaru szczelin lub luzów pomiędzy powierzchniami współpracujących ze sobą części maszyn (rys. 4). Składa się z kompletu 11, 14 lub 20 płytek osadzonych obrotowo jednym
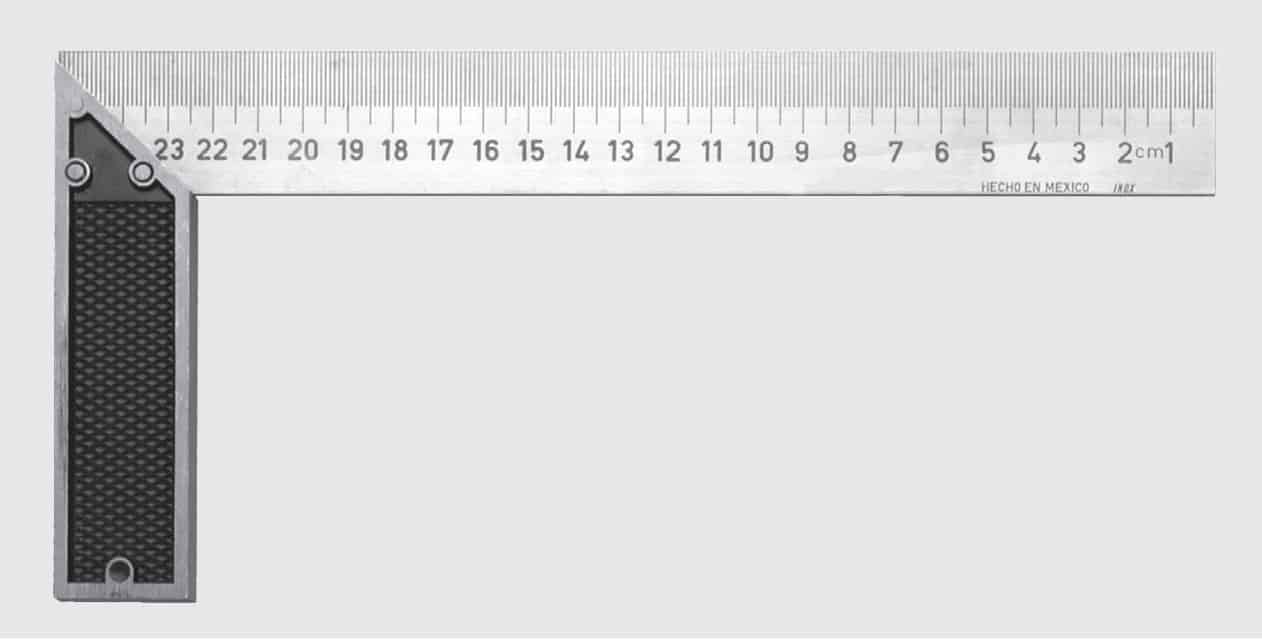
Rys.3. Kątownik ślusarski z grubym ramieniem
Do sprawdzania promieni zaokrągleń wypukłych i wklęsłych stosuje się wzorniki zwane promieniomierzami (rys. 5). Spotyka się komplety promieniomierzy o określonym zakresie pomiarowym. W zestawie takiego kompletu znajdują się płytki o różnych promieniach zaokrąglenia. Każda płytka w zestawie ma uwidocznioną na niej wartość promienia zaokrąglenia. Sprawdzanie np. zaokrąglenia wypukłego polega na przykładaniu kolejnych wzorników tak długo, aż dopasuje się taki, który będzie dokładnie przylegał, lub dobraniu dwóch granicznych, z których płytka z mniejszym promieniem wykazuje szczelinę w środku wzornika, a płytka z większym promieniem – na zewnątrz płytki wzornika.
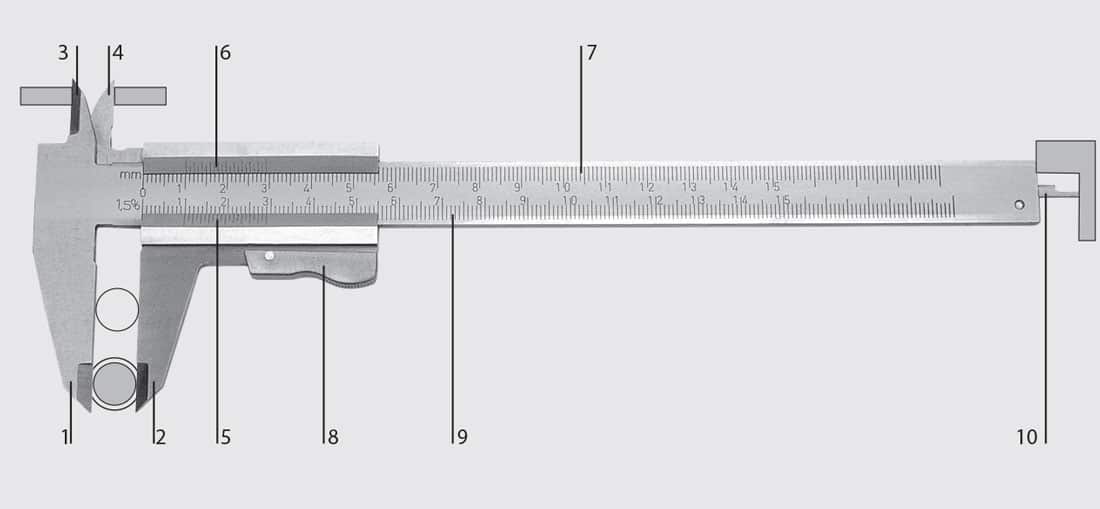
Rys.6. Suwmiarka uniwersalna: 1,2 – szczęki do pomiarów zewnętrznych; 3,4 – szczęki do pomiarów wewnętrznych; 5 – noniusz podziałki milimetrowej; 6 – noniusz podziałki calowej; 7 – podziałka calowa; 8 – dźwignia zacisku; 9 – podziałka milimetrowa; 10 – głębokościomierz (źródło: https://pl.wikipedia.org/wiki/Suwmiarka)tools.pl)
Powszechnie stosowanym i dokładnym przyrządem do pomiarów liniowych jest suwmiarka uniwersalna (rys. 6). Jej uniwersalizm wynika z tego, że można nią wykonywać pomiary zewnętrzne, wewnętrzne oraz głębokości. W praktyce spotyka się suwmiarki z noniuszem, z odczytem za pomocą czujnika i z odczytem cyfrowym. Najczęściej dokładność odczytu pomiaru za pomocą suwmiarki wynosi 0,1 mm lub 0,05 mm. Podstawową częścią suwmiarki jest stalowa prowadnica z podziałką milimetrową zakończona nieruchomą szczęką zewnętrzną i wewnętrzną. Pozostałe szczęki pomiarowe oraz wysuwka głębokościomierza znajdują się na ruchomym suwaku. Na suwaku znajduje się też specjalna podziałka zwana noniuszem. Noniusz suwmiarki o dokładności pomiaru 0,1 mm ma długość 9 mm, ale podzielony jest na 10 części; tak więc działka noniusza ma długość 9/10 mm. Dokonując pomiaru za pomocą suwmiarki, należy do mierzonego elementu dosunąć szczęki pomiarowe i odczytać wymiar na noniuszu. Zerowa kreska noniusza informuje o liczbie całych milimetrów, natomiast dziesiąte części milimetra pokazuje ta kreska noniusza, która jest na przedłużeniu kreski podziałki głównej znajdującej się na prowadnicy. Suwmiarka mierząca z dokładnością 0,05 mm posiada działkę noniusza długości 19/20 mm.
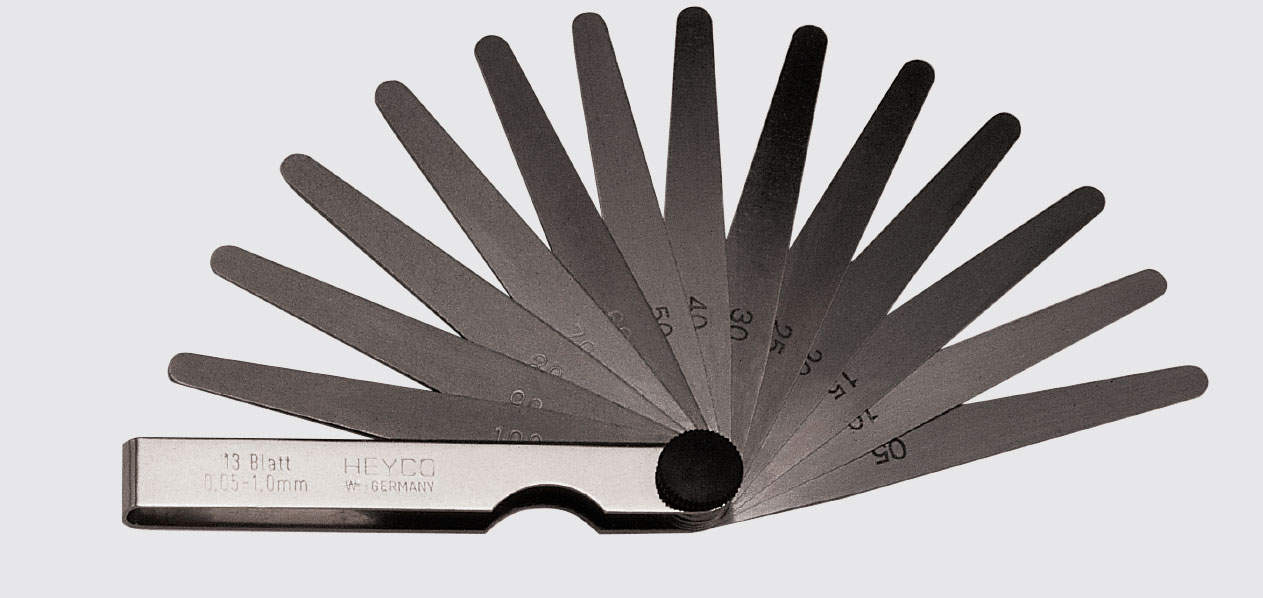
Rys.4. Szczelinomierz (źródło: https://pl.wikipedia.org/wiki/)
Odmianą tradycyjnej suwmiarki jest wysokościomierz suwmiarkowy. Służy on do pomiaru wysokości przedmiotów, odległości punktów lub powierzchni na przedmiocie o kształcie bryły. Warunkiem dokładnego pomiaru jest to, aby zarówno mierzony przedmiot, jak i wysokościomierz były ustawione na tej samej płaskiej powierzchni. Wysokościomierz suwmiarkowy jest przyrządem często stosowanym w trasowaniu przestrzennym po zamocowaniu rysika w miejscu końcówki pomiarowej.

Dokładniejszym od suwmiarki przyrządem pomiarowym jest mikrometr (rys. 7). Używa się go do pomiaru długości, grubości i średnicy z dokładnością 0,01 mm. Jeden koniec kabłąka ma nieruchome kowadełko pomiarowe, a drugi nieruchomą tuleję z kreską wskaźnikową i milimetrową podziałką wzdłużną. Każda milimetrowa działka wzdłużna jest dodatkowo podzielona na połowę. Na tulei jest obrotowy bęben, którego obwód podzielony jest podziałką poprzeczną na 50 równych części. Istotnym elementem mikrometru jest wrzeciono z naciętym gwintem o skoku 0,5 mm. Pełny obrót bębna powoduje przesunięcie wrzeciona o 0,5 mm, a ponieważ jest on podzielony na 50 części to obrócenie bębna o 1 działkę podziałki poprzecznej powoduje przesunięcie wrzeciona o 0,01 mm, co jest dokładnością pomiaru. Wartość mierzonego wymiaru określa się, odczytując na podziałce wzdłużnej liczbę pełnych milimetrów i połówek milimetrów odsłoniętych przez brzeg bębna, a o setnych częściach milimetrów informuje ta kreska na podziałce bębna, która odpowiada wzdłużnej kresce wskaźnikowej na nieruchomej tulei.
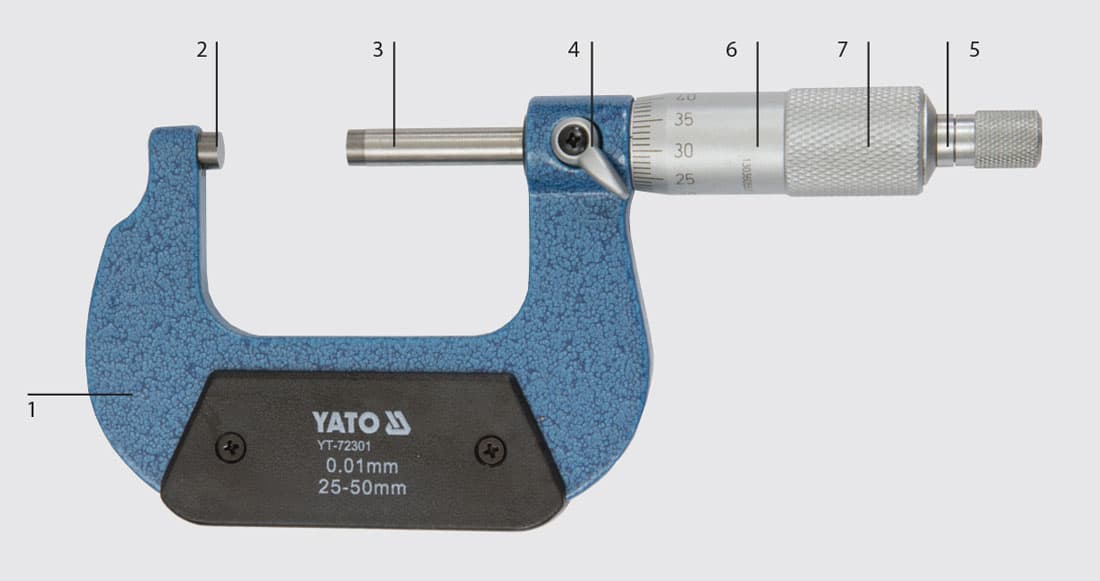
Rys.7. Mikrometr do pomiarów zewnętrznych o zakresie 50-75 mm: 1 – kabłąk; 2 – kowadełko; 3 – wrzeciono; 4 – zacisk; 5 – tuleja; 6 – bęben; 7 – sprzęgło cierne (źródło: https://pl.wikipedia.org/wiki/Mikrometr_(przyrząd))
Aby nie uszkodzić gwintu wrzeciona i dokonać właściwego pomiaru bęben z podziałką obracany jest za pośrednictwem ciernego sprzęgła z pokrętłem. Obracając pokrętłem sprzęgła ciernego, obracamy jednocześnie wrzeciono, do chwili zetknięcia go z mierzonym przedmiotem, który z przeciwległej strony opiera się o nieruchome kowadełko. Jeżeli po dalszym pokręcaniu sprzęgło ślizga się i nie przesuwa wrzeciona należy położenie wrzeciona unieruchomić za pomocą zacisku i odczytać wynik pomiaru.
Do dokładnego wyznaczania wymiarów średnic otworów oraz głębokości otworów nieprzelotowych, zagłębień lub uskoków służą średnicówki i głębokościomierze mikrometryczne. Dokładność pomiarowa obu tych przyrządów wynosi 0,01 mm. W celu zwiększenia zakresu pomiarowego stosuje się odpowiednie przedłużacze.
dr Jan Krzos
Literatura pomocnicza
1. Figurski J., Popis S., Wykonywanie elementów maszyn, urządzeń i narzędzi, WSiP, Warszawa 2015.
2. Górecki A., Technologia ogólna – podstawy technologii mechanicznych, WSiP,
Warszawa 1998.
3. Jakubiec W., Malinowski J., Metrologia wielkości geometrycznych, WN-T, Warszawa2004.
GDZIE MOŻNA KUPIĆ WZORCE DŁUGOŚCI 10mm ;20mmm – nie płytki wzorcowe , w postaci wałeczków o średnicy odpowiednio 10mm i 15mm ( niekalibrowanych ) , w których wzorcowe w/w odległości zawarte są pomiędzy powierzchniami czołowymi tych walców .
Dokładność wykonania takich wzorców powinna być w granicach +/- od 0,001 mm do 0,005 mm .
Czekamy na podpowiedzi internautów. Zachęcamy do wpisów.